Charging Stations for Electric Vehicles
Charging stations and chargers for electric cars and other electric vehicles rely on adhesives: The capacitors, voltage regulators and resistors on the charging boards must be mounted reliably resistant to shock and vibration. With additional conformal coatings, these components can be protected from temperature fluctuations, moisture and other climatic factors.
The same goes for the connector encapsulation in charging cables: Pin sealing protects the sensitive contacts and ensures efficient and fast charging of the batteries in the long term. Adhesives, sealants and casting compounds are ideally suited for these tasks.
The requirements for resistance to environmental influences can depend on many factors: In some cases, hard, resistant epoxy resins are required; in others, a more flexible, low-stress connection is preferred. Beside environmental conditions, the choice of casting or bonding compound is determined by factors such as substrates, surface characteristics and coefficients of thermal expansion of the materials used.
The choice of process can also affect the product recommendation. Especially UV-curing products enable a particularly efficient and rapid bonding process. For bonding applications with shaded zones that cannot be reached by light, the dual-curing products provide the most reliable curing results.
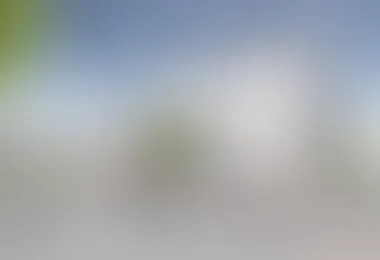
Adhesives protect the electronics in charging stations and chargers
Download:
In the following table you will find a selection of adhesives suitable for bonding in charging stations and chargers. Other products and customer-specific solutions are available on request.
Technical data sheets can be downloaded by clicking on the adhesive name.
Adhesive | Viscosity [mPas] | Base | Curing* | Properties |
---|---|---|---|---|
Vitralit® 1600 LV | 3,000-5,000 | epoxy |
UV secondary heat cure |
Very high Tg low water absorption low ion content very high chemical resistance |
Vitralit® UD 8050 | 8,000-11,000 | acrylate |
UV VIS secondary moisture cure |
Isocyanacrylate fast moisture post-curing in shadowed areas easy to dispense with jet or dispenser e.a. resistant to moisture fixing and protecting electronic components |
Vitralit® UD 8050 LV | 200-400 (Rheometer, 25°C, 5s^-1) | acrylate |
UV, VIS, moisture postcuring |
Moisture post-curing in shadowed areas; tack-free surface |
Vitralit® FIPG 60102 | 100,000-250,000 (Rheometer, 25°C, 10s^-1); 15,000-40,000 (Rheometer, 25°C, 1s^-1) | acrylate |
UV VIS |
Flexible/elastic liquid gasket, high resilience, easy to apply, fast curing with UV light |
Vitralit® 6300 | 2,500-4,000 | acrylate |
UV VIS secondary heat cure |
jetable non-yellowing very high adhesion to glass and metals dual cure |
Structalit® 3060 N | 4,000-8,000 (Rheometer, 25 °C, 10^s-1) | epoxy | thermal |
non-conductive high flexibility very fast curing very low ion content |
Structalit® 5800 | 12,000-22,000 part A (LVT 25°C, Sp. 4/12 rpm); 500-800 part B (LVT 25°C, Sp. 2/30 rpm); 7,000-15,000 mix (LVT, 25°C, Sp. 4/30 rpm) | 2-part epoxy | thermal, room temperature |
High temperature resistance short pot life fast application |
Structalit® 5810-1 | 1,000-1,500 part A (LVT 25°C, Sp. 3/30 rpm); 3,500-4,500 part B (LVT 25°C, Sp. 4/30 rpm); 3,000-4,000 mix (LVT, 25°C, Sp. 4/30 rpm) | 2-part epoxy |
thermal room temperature |
Very high adhesion to PC resistant to moisture and chemicals |
Structalit® 5811 | Part A: 900-1,300, Part B: 100-350 | 2-part epoxy | thermal, room temperature | Very good adhesion to metals, glass and many plastics |
Structalit® 8801 | 30,000-45,000 (LVT, 25°C, Sp. 4/6 rpm) | epoxy | thermal |
Resistant to oils, grease and fuels excellent flow properties beige color certified to ISO 10993-5 standards |
Penloc® GTI | 4,000-6,000 part A, part B (LVT, 25 °C), 5,000 mix (LVT, 25 °C, Sp.4 / 30 rpm) | 2-part-acrylate | room temperature | Fast curing |
Penloc® GTH-T | 8,000-10,000 part A, part B, mix (LVT, 25 °C, Sp.4 / 30 rpm) | 2-part-acrylate | room temperature |
Very high adhesion to metal temperature resistant |
*UV = 320 - 390 nm VIS = 405 nm