Conformal Coatings
A conformal coating is used to protect electronic components from environmental factors. Adhesives used as conformal coatings are dual-curing: at their edges and visible surfaces they are cured with UV light; the shadowed areas – for example underneath components or chips – as well as deeper-lying regions are then post-cured by heat application.
To cover large surfaces with a conformal coating, we recommend low-viscosity adhesives. These adhesives are equally suited for spray coating, spin coating and dip coating.
Selective conformal coating can be realized with high-viscosity dam material: With a highly viscous adhesive, a frame or dam is formed, which is then filled with mobile adhesive. This process is also referred to as frame-and-fill.
UV-curing conformal coatings allow rapid curing resulting in the advantage of inline processing methods. Especially epoxy resin-based adhesives are silicone-free and ensure maximum media resistance.
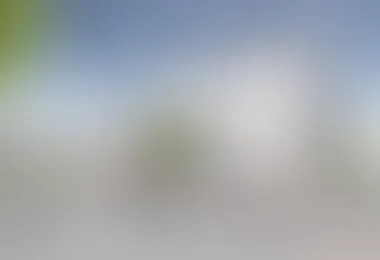
Fluorescent uv epoxy adhesive is used as conformal coating on a PCB
The table below lists a selection of Panacol adhesives suitable as conformal coating. Further products and custom solutions are available on request.
To download the technical datasheets (TDS) please click on the adhesive name.
Adhesive | Viscosity [mPas] | Base | Curing* | Properties |
---|---|---|---|---|
Vitralit® 1671 | 9,000-14,000 (Rheometer, 10s^-1) | epoxy |
UV secondary heat cure |
Stable frame compound high ion purity electronic grade adhesive high temperature conductivity low water absorption UL94 HB test passed |
Vitralit® 2004 F | 60-100 (LVT, 25 °C, Sp. 2/30 rpm) | epoxy |
UV secondary heat cure |
fluorescing flexible autoclavable dry surface after curing low ion content sprayable |
Vitralit® 2007 F | 150-350 (LVT, 25 °C, Sp. 2/30 rpm) | epoxy |
UV secondary heat cure |
fluorescing flexible autoclavable excellent chemical resistance low ion content |
Vitralit® 2028 | 160-300 | epoxy |
UV secondary heat cure |
Dry surface after UV-curing autoclavable excellent chemical resistance scratch resistant coating |
Vitralit® 2009 F | 100-200 | epoxy |
UV secondary heat cure |
fluorescing flexible autoclavable high chemical resistance low ion content |
Vitralit® 4451 MV F | 2,000-3,000 (LVT, 25 °C, Sp. 4/30 rpm) | acrylate | UV, VIS |
soft and elastic dry surface after curing protective coating fast curing fluorescing blue |
Vitralit® UD 8050 | 8,000-11,000 (Rheometer, 25 °C, 5s-1) | acrylate |
UV VIS secondary moisture cure |
Isocyanacrylate; fast moisture post-curing in shadowed areas; easy to dispense with jet or dispenser e.a.; resistant to moisture; compatible with flux |
Vitralit® UD 8055 | 5,000-8,000 (Rheometer, 25°C, 10s^-1) | acrylate |
UV VIS moisture cure |
High Tg Fast curing Compatible with flux Low ion content |
Vitralit® UD 8056 | 3,000-6,000 (Rheometer, 25°C, 10s^-1) | acrylate | UV / VIS / Moisture postcuring |
High Tg, fast curing Compatible with flux Low ion content Passed UL94 HB test |
*UV = 320 - 390 nm